Unlocking the Potential of custom bolts in Modern Manufacturing
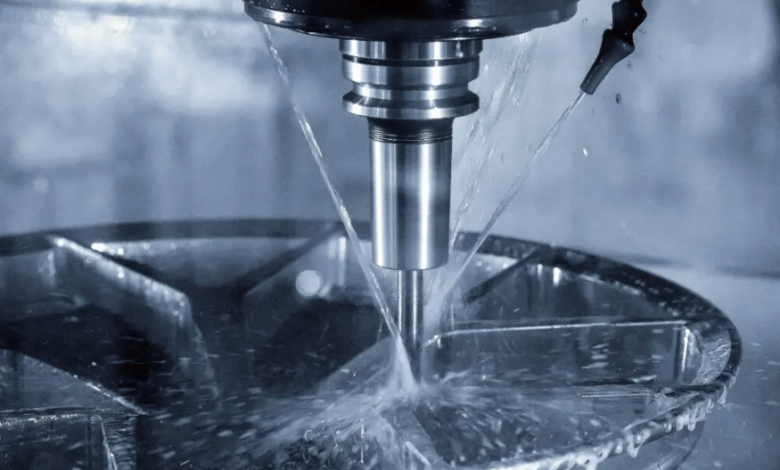
In the fast-evolving landscape of manufacturing and engineering, precision and customization have become critical factors in product development. Among the many components that define a product’s strength and durability, bolts play a pivotal role. While standard bolts are widely used, there is a growing demand for custom bolts tailored to meet specific application requirements. These specially designed fasteners offer unparalleled performance, reliability, and flexibility across various industries.
This article explores the significance of custom bolts, their benefits, manufacturing processes, and how businesses can leverage them to enhance product quality and innovation.
What Are custom bolts?
Custom bolts are fasteners manufactured according to specific design, size, material, and finish requirements that differ from standard off-the-shelf options. They are crafted to address unique engineering challenges such as unusual load conditions, environmental factors, or proprietary design constraints.
Unlike generic bolts, custom bolts can have:
- Unique dimensions and thread patterns
- Specialized head shapes and drive types
- Tailored material compositions and heat treatments
- Custom coatings for enhanced corrosion resistance
These adaptations ensure the bolts precisely fit the intended application and perform optimally.
See also: Use Massage To Make Every Business Trip A Little More Pleasant
Why Choose custom bolts Over Standard Fasteners?
1. Tailored to Exact Specifications
Custom bolts can be designed to meet the precise mechanical and dimensional needs of your project, ensuring perfect compatibility and eliminating fitment issues.
2. Superior Performance in Challenging Environments
Special materials and surface treatments allow custom bolts to withstand extreme temperatures, corrosive chemicals, heavy vibrations, or high tensile stresses.
3. Compliance with Industry Standards and Regulations
Many sectors such as aerospace, automotive, and medical require fasteners certified to strict standards. Custom bolts ensure adherence to these certifications with full traceability.
4. Cost Efficiency Over the Product Lifecycle
Though initially more expensive, custom bolts reduce maintenance needs, prevent failures, and lower warranty costs by delivering greater durability and reliability.
5. Intellectual Property and Brand Differentiation
Custom bolt designs can include unique markings, proprietary thread forms, or security features to protect your product’s identity and reduce counterfeiting risks.
Typical Applications of custom bolts
Custom bolts find use across many industries where specialized requirements exist:
- Aerospace: Lightweight, high-strength alloys and precision threads for safety-critical components
- Automotive: Corrosion-resistant bolts for engine parts and suspension systems
- Construction: Heavy-duty bolts designed for load-bearing structural applications
- Electronics: Miniature bolts with fine threads for compact assemblies
- Medical Devices: Biocompatible materials and sterile finishes for implants and instruments
Manufacturing Process of custom bolts
The production of custom bolts involves several key steps to ensure precision and quality:
1. Design and Engineering
Collaboration between manufacturers and engineers determines bolt specifications, material selection, and performance requirements.
2. Material Procurement
Raw materials such as alloy steel, stainless steel, titanium, or brass are sourced based on application demands.
3. Forming and Machining
Depending on volume and complexity, bolts are formed using cold heading for large runs or CNC machining for custom shapes and low volumes.
4. Threading
Threads are rolled or cut with high precision to ensure strength and fit.
5. Heat Treatment
Bolts undergo heat treatment processes to achieve desired mechanical properties like tensile strength and hardness.
6. Surface Finishing
Coatings such as zinc plating, galvanization, anodizing, or specialized corrosion-resistant layers are applied.
7. Quality Inspection
Dimensional checks, mechanical testing, and surface inspections confirm compliance with specifications.
8. Packaging and Delivery
Bolts are packaged per client requirements, ensuring protection during transit and ease of handling.
Advantages of Working with a Custom Bolt Manufacturer
Expertise and Collaboration
Custom bolt manufacturers often provide engineering support, helping optimize bolt design for performance and manufacturability.
Flexibility
Manufacturers can handle both prototype runs and mass production, adjusting processes to fit timelines and budgets.
Quality Assurance
Certified quality systems and rigorous testing guarantee consistent performance and regulatory compliance.
Supply Chain Integration
Many manufacturers offer logistics support, including just-in-time delivery and inventory management, reducing overhead for clients.
How to Select the Right Supplier for custom bolts
When choosing a supplier for custom bolts, consider the following:
Selection Criteria | Key Considerations |
Industry Experience | Expertise in your sector and familiarity with relevant standards |
Technical Capabilities | Ability to produce complex designs and materials |
Certifications | ISO 9001, ASTM, and other industry-specific accreditations |
Quality Control | Processes for inspection, testing, and traceability |
Manufacturing Capacity | Scalability from prototypes to mass production |
Customer Support | Communication, responsiveness, and problem-solving skills |
Logistics and Delivery | Timeliness and packaging tailored to your needs |
Request samples and visit production facilities if possible to validate capabilities.
Case Study: Elevating Performance with custom bolts
A renewable energy company required bolts capable of withstanding harsh offshore environments with saltwater exposure and heavy mechanical loads. Standard bolts corroded prematurely, leading to frequent maintenance shutdowns.
Collaborating with a custom bolts manufacturer, they developed:
- Bolts made of high-grade duplex stainless steel
- Special anti-corrosive coatings applied using advanced processes
- Custom dimensions and threads optimized for assembly efficiency
This solution extended bolt life significantly, reduced maintenance costs, and improved overall system uptime.
Future Trends in custom bolt Manufacturing
Smart Fasteners
Embedding sensors in bolts for real-time monitoring of stress, torque, and environmental conditions is an emerging innovation.
Advanced Materials
The adoption of new alloys and composites enhances strength-to-weight ratios and environmental resistance.
Additive Manufacturing
3D printing enables rapid prototyping and production of complex bolt geometries that were previously difficult to manufacture.
Sustainable Practices
Eco-friendly materials and waste reduction strategies are gaining importance in bolt manufacturing.
Conclusion
Custom bolts are indispensable for modern manufacturing industries that demand precision, performance, and compliance. By investing in tailor-made fasteners designed to exact specifications, businesses unlock benefits ranging from enhanced product reliability to reduced lifecycle costs.
Partnering with a skilled custom bolts manufacturer ensures access to engineering expertise, advanced manufacturing technologies, and stringent quality control. This collaboration empowers companies to meet the toughest challenges and stay competitive in today’s dynamic markets.